Intelligent Supervision
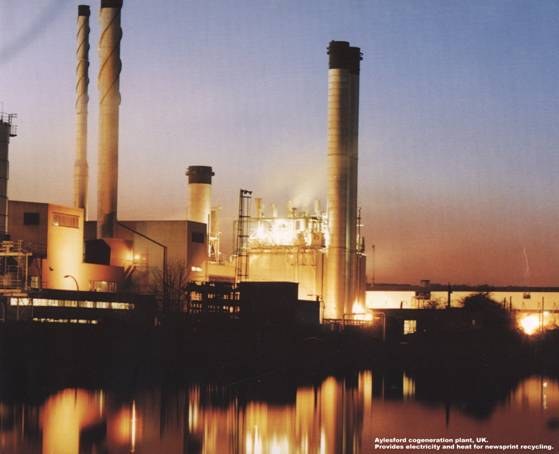
Modern society depends strongly upon the availability and correct operation of complex technological systems (cars, planes, trains, etc.) and processes (water and energy distribution networks, chemical factories, ...). Due to the simultaneously increasing economic demands and the numerous ecological and safety restrictions to be met, high dependability of those systems and processes has become a dominant goal in the recent years. However, malfunctions (or fault) can appear causing economic losses, damage to operators and machines, disturbance to the users, etc. In a general sense, a fault is any change in the behaviour of any component of the system.
In order to increase reliability, safety and availability of a system, the CER CS2AC-UPC works to develop new methodologies and intelligent supervision tools that make possible:
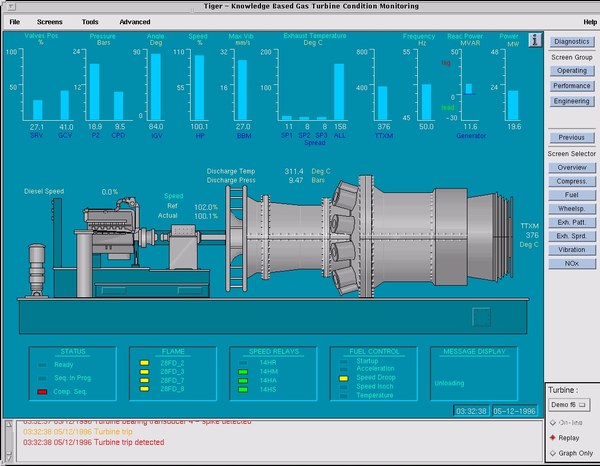
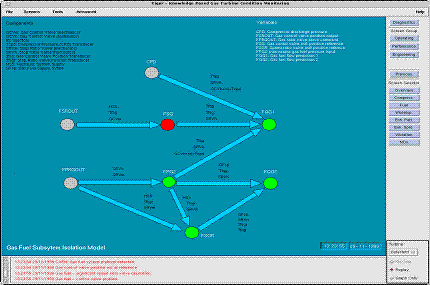
Complex technological systems and processes are subject to a number of requirements:
- They have to operate continuously over long periods of time and with a minimal intervention of the operator;
- The cost derived from faults and problems maintenance must be reduced;
- Must be supervised by operators that could be not very specialized and can be remotely controlled.
To fulfil these requirements a supervising system that monitors and improves the availability of the plant avoiding downtime and unplanned system failures was needed. The requirements of this system are:
- They have to work in a continuous way for long periods of time, and with the minimum intervention of the operators;
- The cost derived from failures and problems of maintenance has to be low;
- It is necessary that they can be supervised by not really prepared and specialized operators and remotely controlled, since these plants are installed in a great diversity of countries.
More concretely, the research carried out by the CER CS2AC-UPC within this area is:
- To develop representative models of the behavior of the systems or processes, capable of distinguishing between a normal behavior or a behavior in failure.
- To define strategies based on models able to allow to locate failures.
- To distinguish the degree of diagnosis of a system or process from the measurable variables.
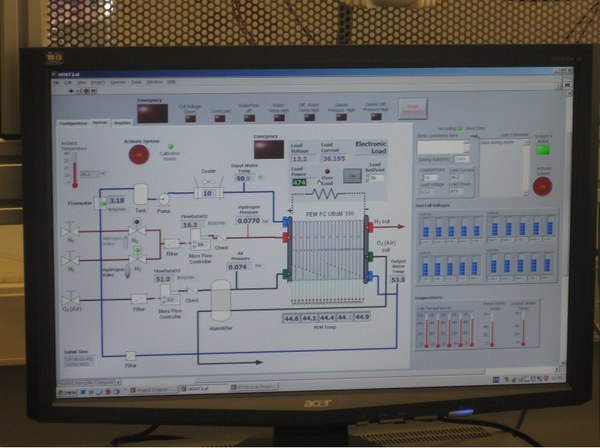
The tolerance to failures it is then understood as the capacity of a control system to maintain the objectives of control, in spite of the appearance of a failure, accepting a certain degradation of its benefits.
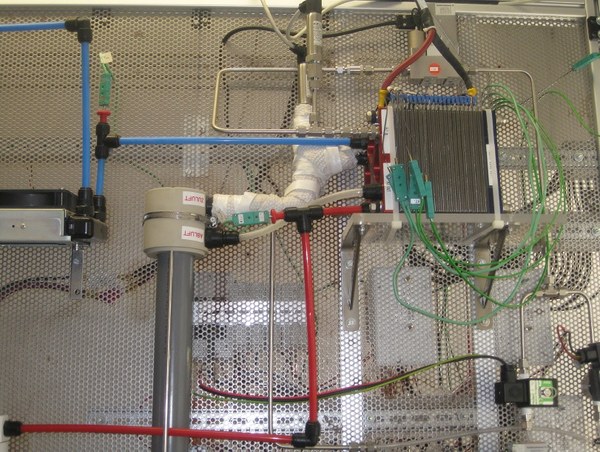
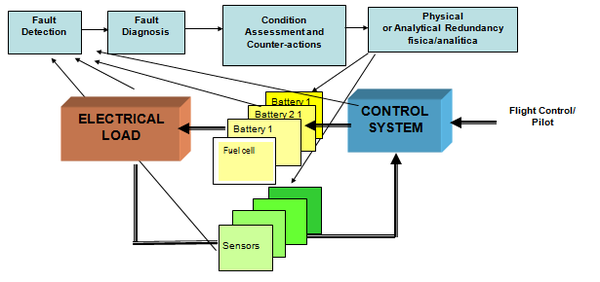
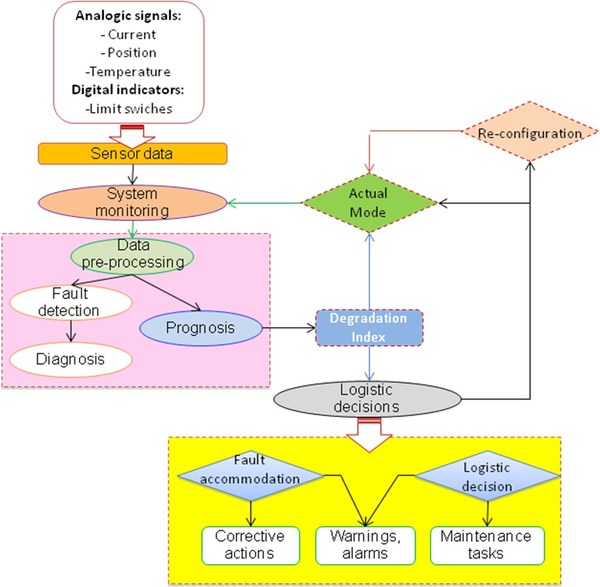
These thecniques are being applied in a wide variety or real processes and laboratory, such as: wind turbines, UAVs, gas turbines, water distribution networks, fuel cell, ....
Share: