TIGER-SHEBA
ESPRIT Trial Application no. 27548, 1998 - 2000.
Objectives
Develop a monitoring system with the following features:
- Continuously observe the working conditions of the gas turbine.
- Detect the development of a failure or problems as early as possible.
- And when a problem is detected, diagnose it as quickly and accurately as possible (cause).
Summary
Gas turbines are the key element in energy-generating industries. Currently, new power plants are being built relatively quickly and economically. Users need certain requirements in this increasingly competitive energy market:
- Gas turbines must operate continuously for long periods with minimal operator intervention.
- The cost derived from failures and maintenance problems must be low.
- They must be supervisable by operators who are not highly trained or specialized and must be remotely controlled, as these plants are installed in a variety of countries.
- The cost derived from failures and maintenance problems must be low.
- They must be supervisable by operators who are not highly trained or specialized and must be remotely controlled, as these plants are installed in a variety of countries.
To meet these requirements, a supervisory system is needed to increase the plant’s availability and avoid downtime, as well as unplanned system failures. In case of failure, the system must minimize downtime.
The main requirement of the supervisory system is to detect problems at the early stage and act before the failure becomes catastrophic for the turbine. If an unexpected failure occurs, the system must quickly indicate the component or part of the process where the issue is, so the plant can return to energy production as quickly as possible. Another factor to consider is ensuring the machine operates with optimal efficiency, as a machine typically consumes 1.5 million USD in gas each month, so a 1-2% decrease in efficiency can result in high costs.
The TIGER-SHEBA monitoring system has been developed to meet these requirements. It receives around 600 measurements from the gas turbine controller every second and performs fault detection and diagnosis in this time. Initially, the monitoring system included a rule-based system for detecting faults and a diagnostic system combining temporal rules and hierarchical abstraction. This methodology requires everything to be pre-programmed, so any new situation that hasn't been studied "a priori" and defined with a rule becomes an unknown situation that cannot be diagnosed. For this reason, a more advanced methodology (referred to as the second generation of knowledge-based systems) has been incorporated into the turbine diagnostics, using representative models of the turbine’s behavior to identify known and unknown discrepancies between the real system and the model.
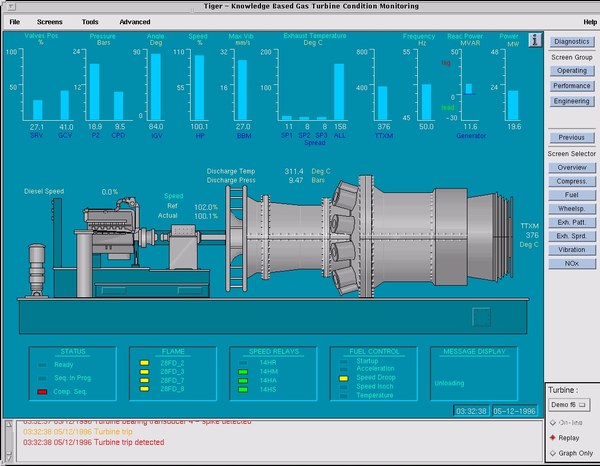
The TIGER-SHEBA system incorporates models for fault detection and diagnosis, continuously comparing the signals provided by the sensors with the model variables, generating what are called residuals or discrepancies between the real system and the models.
If the turbine is working correctly and the models are representative, the residuals are practically zero. However, if a malfunction occurs, the residuals will be different from zero, indicating a problem.
If the turbine is working correctly and the models are representative, the residuals are practically zero. However, if a malfunction occurs, the residuals will be different from zero, indicating a problem.

The main objective of the project has been to incorporate interval qualitative models based on the Ca~En methodology. This combines the fault detection capacity based on models, which predicts the output variable values, with fault isolation mechanisms based on models.
Model-based fault detection and diagnosis has been applied to critical subsystems of the gas turbine, such as the liquid and gas fuel feeders. Figure 6 shows the fault isolation scheme for the liquid fuel supply system. The Ca~En isolation module generates diagnostic messages, which are displayed in the TIGER diagnostic window.
Model-based fault detection and diagnosis has been applied to critical subsystems of the gas turbine, such as the liquid and gas fuel feeders. Figure 6 shows the fault isolation scheme for the liquid fuel supply system. The Ca~En isolation module generates diagnostic messages, which are displayed in the TIGER diagnostic window.
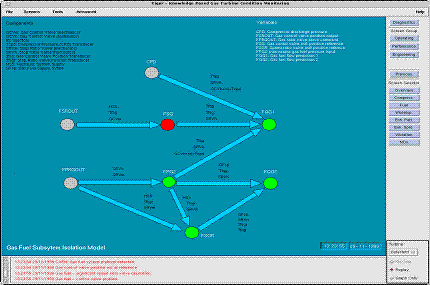
Research Group
Joseba Quevedo*, Louise Travé-Massuyès**, Teresa Escobet* and Sebastian Tornil*
* Professors at the Polytechnic University of Catalonia.
** Research Director at CNRS, member of the "Diagnostic, Supervision, and Qualitative Control" group of LAAS-CNRS in Toulouse (France)
For more information:
A more detailed summary of the project results can be found in: Resultats_tiger_sheba.pdf and the description of the methodology used in Article_tiger_sheba.pdf
Share: